Common Questions
Steel reinforced rods which mainly contains Iron (Fe) is stable only in the oxide form which is the original form of existence when obtained from ore. From the ore stage, Fe is refined and subjected to various cold and hot process (i.e., addition / imparting of energy) before made it in to reinforcement rods. In this stage, Fe try to release the added energy (release of electrons) and go back to its original form (i.e., oxide form). This continuous oxide formation in the steel is called as rusting. Therefore corrosion of steel is a natural phenomenon which cannot be prevented but can be controlled. Application of anticorrosive coating to steel rebar is one of the corrosion control measure.
Corrosion of steel rods inside the concrete is electrochemical in nature. The weak spots in the reinforcement rods act as anode and the remaining area of steel act as a cathode. The pore water inside the concrete will act as an electrolyte. Once this phenomenon is established, steel rebar in the anode portion corrodes heavily (i.e., releasing electrons), leads to increase in volume / size / diameter of rebar. This causes tensile stresses to the surrounding concrete. If the tensile stresses developed is more than the tensile strength capacity of concrete, the concrete develop cracks results in spalling or complete removal from the concrete member. Presence of chlorides in the concrete and carbon-di-oxide in the surrounding aggravates the electro chemical activity and leads to premature failure of the Reinforced concrete member.
This can be well understood by understanding the mechanism of formation of concrete. The basic ingredient materials used for manufacture of concrete are cement, sand, jelly (coarse aggregate) and water. In this sand and jelly are highly inert materials. The other ingredients cement and water react with each other (hydration reaction) results in evolution of heat and subsequent cement hydrate (jel) formation. These hydrates encompasses the inert sand and jelly and concrete is formed. From the research studies, it is proved that the hydration reaction will continue / takes place for several years and need of water for the same.
Therefore, early age concrete is not fully impenetrable and absorbs water. The various ways of chloride ingress in to concrete are through concrete mixing water; sand /jelly containing chlorides and curing water with chloride content. In marine conditions, the presence of chloride in the saturated air permeate through concrete pores and leads to corrosion of steel rods.
CORROCON -CPAC is the simple nano phased cement polymer anticorrosive coating system which is amenable to small construction site to major projects executed in congested urban locations. This system requires simple loose rust removal from the steel rods using steel wire brush and subsequent application of one / two coats of CORROCON-CPAC mixed cementious slurry. In case of factory fresh reinforcement rods with blue oxide layer (rust free), there is no need for surface cleaning. This coating system forms a passivation layer over the reinforcement rods and controls rusting of steel rebars.
Whereas most of the commercially available anticorrosive coating systems requires acid pickling / sand blasting / shoot blasting types of surface cleaning which is highly cumbersome and not practically feasible in the infrastructure projects executed under urban areas. Moreover current environmental norms strongly objects usage of picking / sand blasting / shoot blasting process in potential areas.
Most of the coatings are designed as factory oriented process which involves multiple procedures and added with unnecessary transportation expenses and subject to the risk of damage to coating during transportation. Whereas CORROCON coating system is site oriented which needs only a small working space. Since it is a simple process, quality control can be achieved with less prone to coating damage.
- Even a small quantity of steel reinforcement rods can be given anticorrosive treatment with optimum amount of CORROCON - CPAC solution and ideally suits for individual buildings constructed by a common man.
- No major infrastructure facilities are required. The facilities available in the construction site can be effectively utilized for coating application.
- Ideal treatment process for providing anticorrosive treatment to existing corroded steel reinforcement rods.
- Although a simple system, satisfy the most of the requirements of Indian / ASTM codal provisions for coated rebars.
Incorporation of corrosion inhibiting admixture in concrete is one of the effective methods of controlling corrosion of steel rods inside the concrete environment. Where buildings constructed in a congested location with space constraint, MOONCRETE-CI : Corrosion inhibiting admixture can be added at 1 - 2% by weight of cement in the fresh concrete to provide corrosion protection to uncoated steel rods embedded in the concrete. The dosage of addition of corrosion inhibitor varies according to expected chloride threshold limit for the particular environment.
In addition to corrosion protection, addition of MOONCRETE offers improved workability of concrete at lesser water cement ratio as compared to control concrete. Hence significantly increases the compressive strength, reduces the water penetration and improves the resistance against chloride penetration of the concrete matrix.
Concrete in the early ages is not fully resistance against water penetration. The hydration process (reaction between cement and water) takes place over several decades although close to 90% hydration reaction happens at 28 days. This reveals that concrete is in need of water for hydration reaction. Hence no more concrete is fully waterproof.
The reinforced concrete elements such as sunken slab, terrace slab, sunshade etc. are exposed to water which mandates provision of effective water proofing treatment on these members and other salient locations in the building.
The usual construction practice adopted in the sunken area is that sanitary arrangements are placed in the sunken slab and covered with brick jelly concrete. This followed with placing bed mortar and laying of ceramic tiles. The tile joint are given with white cement packing.
While at use, due to removal of white cement packing in the tile joints, allows the water to penetrate. The brick jelly concrete absorbs the entering water to its full limit and allows the water to further seeps through the sunken slab. Therefore it is necessary to provide effective waterproofing treatment over the sunken slab by providing proper slope towards the exit spout pipe.
In India, brick bat coba packed with cement mortar / brick bat jelly concrete is laid over the mother terrace slab to a thickness of 4 - 5" as a weathering course to dissipate incident heat. This follows with laying of cement mortar bedding mortar and clay / country tile. The tile joints are pointed with rich cement mortar paste.
In practice, due to variation in thermal expansion / contraction exhibited between brick bat coba , clay tile topping and mother concrete slab, cracks develops in the clay tile layer. This allows entry of water during raining seasons and completely soaks the brick bat coba / brick jelly concrete and causing dampness / water leakage to terrace concrete slab beneath.
Therefore it is vital to provide water proofing treatment to mother terrace slab before laying brick bat coba / brick jelly concrete over it.
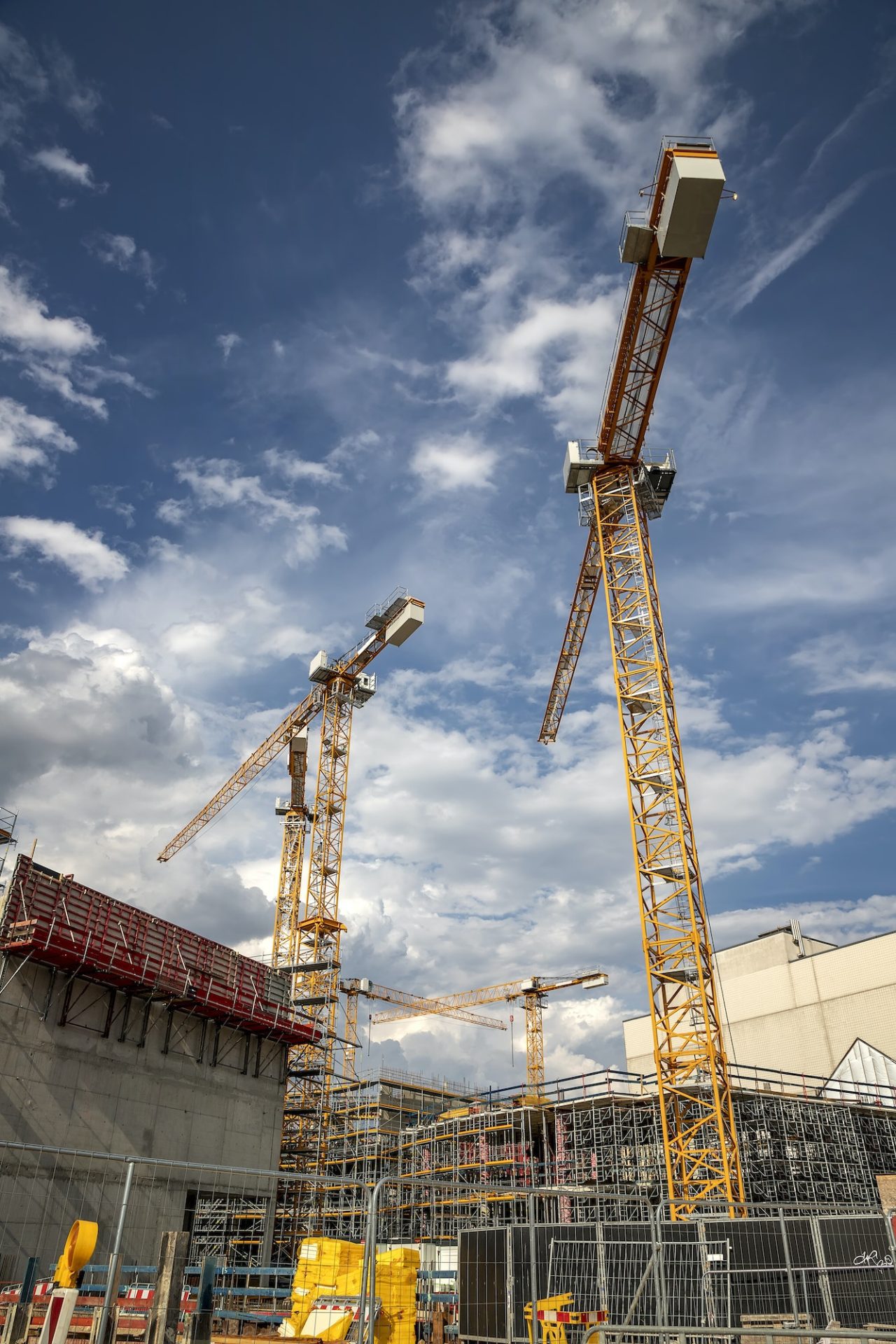